Przenośniki, zautomatyzowane reach trucki i regały w Lajkonik
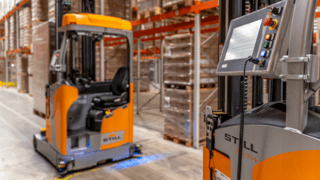
W ramach kompleksowej rozbudowy i modernizacji zakładu produkcyjnego Lajkonik Sp. z o.o. dokonano automatyzacji magazynu. Procesy transportu wewnętrznego i składowania oparto o technologie automatyzacyjne firmy STILL.
Na skróty:
-
W związku ze wzrostem popytu na jej produkty, spółka Lajkonik Snacks planowała rozbudowę i modernizację magazynu stanowiącym część kompleksu produkcyjnego w małopolskiej Skawinie.
-
Firma poszukiwała rozwiązania automatyzacji magazynu, które pozwoli zwiększyć przepustowość zakładu, będzie charakteryzować się niskim wskaźnikiem TCO i w efekcie szybko się zwróci.
-
Lajkonik Snacks sp. z o.o. zdecydowała się na wdrożenie zaproponowanego przez firmę STILL Polska całościowego rozwiązania bazującego na użyciu: przenośników, samojezdnych wózków wysokiego składowania STILL FM-X wraz z komputerowym systemem zarządzania, regałów wysokiego składowania oraz – komplementarnie – wózków prowadzonych ręcznie.
-
Inwestycja pozwoliła zwiększyć liczbę obsługiwanych ładunków bez potrzeby zwiększania zatrudnienia. Uzyskane wskaźniki spełniły oczekiwania firmy Lajkonik.
Charakter przedsiębiorstwa, w którym dokonano wdrożenia
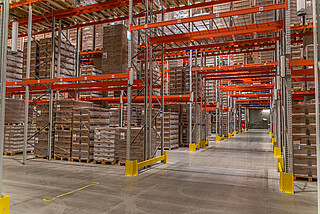
Nazwa: Lajkonik Sp. z o.o.
Obszar działalności: Przemysł spożywczy - produkcja słonych przekąsek
Miejsce wdrożenia: Skawina, Polska
Lajkonik Snacks sp. z o.o. to przedsiębiorstwo z ponad 100-letnią tradycją. Podstawowym obszarem jego działalności jest wytwarzanie przekąsek słonych takich jak paluszki, precelki, krakersy i talarki. Firma jest liderem rynku w Polsce, a jej produkty są eksportowane do niemal 80 krajów na całym świecie. Elementem przeprowadzonej w ostatnich latach kompleksowej rozbudowy i modernizacji zakładu Lajkonik było wzbogacenie obiektu o wydajny i bezpieczny zautomatyzowany magazyn wysokiego składowania umożliwiający utrzymanie niskiego wskaźnika TCO floty wózków widłowych przy pracy ciągłej.
Zakład firmy Lajkonik znajduje się w małopolskiej Skawinie. Ze względu na rosnący popyt na produkty zdecydowano się na jego kompleksową rozbudowę. W toku inwestycji zwiększono powierzchnię oraz zmodernizowano m.in.: halę produkcyjną z częścią socjalną oraz halę magazynową wysokiego składowania wraz z halą doków rozładunkowych. Ostatecznie uzyskano zabudowę o powierzchni użytkowej 9 662 mkw. i kubaturze 136 181 m3.
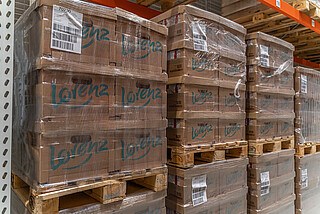
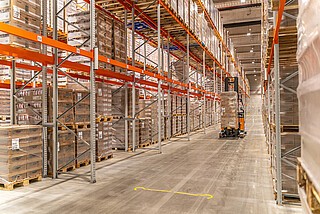
Rozwiązanie: całościowa automatyzacja magazynu
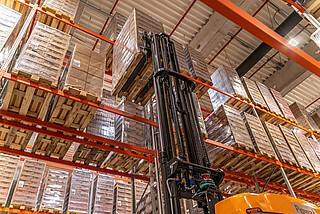
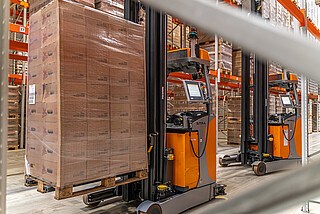
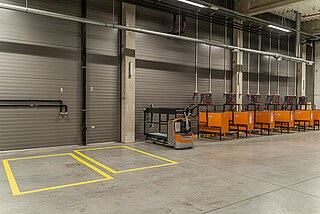
Cel wdrożenia:
- Zwiększenie przepustowości magazynu bez zwiększania zatrudnienia
- Uzyskanie niskiego wskaźnika TCO floty intralogistycznej w pracy ciągłej
- Wypracowanie szybkiego zwrotu z inwestycji
Zastosowane rozwiązanie intralogistyczne:
- System regałów wysokiego składowania STILL,
- Automatyczne boczne wózki wysokiego składowania STILL FM-X,
- Zindywidualizowany system Traffic Manager,
- Stacje ładowania okazjonalnego i akumulatorownia STILL
Głównym kryterium wyboru partnera biznesowego modernizacji magazynu były: uzyskanie wysokiej efektywności procesów składowania oraz niskie koszty eksploatacji maszyn. Zautomatyzowano transport i składowanie produktów gotowych – od podjęcia ładunków z produkcji aż po ich przygotowanie do wysyłki. W tym celu wykorzystano system złożony z szeregu komplementarnych rozwiązań. Jego pierwszym elementem są przenośniki, dzięki którym spaletyzowane towary trafiają z linii produkcyjnych do magazynu. Odbywa się na nich automatyczna weryfikacja wymiarów palety. Tylko poprawne ładunki trafiają do magazynu wysokiego składowania. Zweryfikowane pozytywnie palety są podejmowane i transportowane z punktu poboru z użyciem automatycznych wózków wysokiego składowania serii STILL FM-X. Samobieżne pojazdy AGV wybierają optymalne trasy i bezpiecznie transportują ładunki do systemu regałowego. W zastosowanym w zakładzie Lajkonika systemie regałowym wysokiego składowania najwyżej położone półki znajdują się na poziomie 8 100 mm. System ma łącznie 7 145 miejsc paletowych. Odpowiednie miejsce składowania przydzielane jest za pomocą naszego systemu zarządzania wózkami z modułem WMS.
W zakładzie wdrożono hybrydowy system ładowania akumulatorów zautomatyzowanych wózków widłowych. Gdy pojazdy nie realizują zleceń, samodzielnie udają do jednej z czterech stacji ładowania okazjonalnego, gdzie bez udziału personelu są w stanie uzupełniać baterie. W przypadku dużego obciążenia pracą, możliwe jest także zlecenie wózkom zjeżdżania do akumulatorowni, gdzie dokonuje się manualnej wymiany baterii. Między innymi w tym celu w zakładzie zastosowano system Traffic Manager dostosowany do oczekiwań klienta. Rozwiązanie stanowi intuicyjny interfejs, dzięki któremu składa się zlecenia wózkom automatycznym, co daje to elastyczność i możliwość dostosowania pracy AGV do zmieniających się sytuacji.
Dobrym przykładem synergii pomiędzy pojazdami automatycznymi a wózkami sterowanymi ręcznie jest także proces załadunku palet na samochody ciężarowe. Po przyjęciu z systemu SAP listy palet do wysyłki, AGV pobierają z regałów zgodne z zamówieniem ładunki i gromadzą je w układzie blokowym w strefie wysyłki przy odpowiednim doku. Stąd pracę przejmują operatorzy w wózkach sterowanych ręcznie. To oni dokonują załadunku na naczepę, gdy w doku pojawi się ciężarówka. Wyposażenie wózków automatycznych w specjalny sterownik połączony ze skanerami laserowymi gwarantuje bezpieczeństwo, dzięki czemu nie było potrzeby wydzielania obszaru ich pracy.
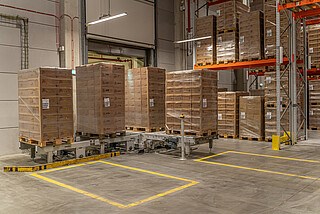
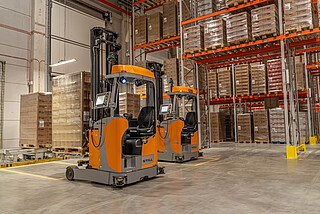
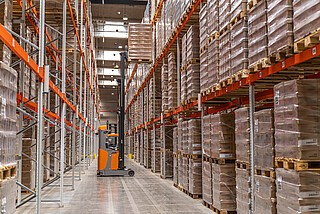
Efekt: efektywna praca magazynu i szybki zwrot z inwestycji
Rezultat wdrożenia:
-
Efektywne wykorzystanie przestrzeni magazynowej dzięki wykorzystaniu systemów regałowych wysokiego składowania.
-
Zwiększenie przepustowości magazynu bez konieczności zatrudniania dodatkowych pracowników.
-
Uzyskanie niskiego wskaźnika TCO i krótkiego czasu zwrotu z inwestycji
-
Optymalne połączenie rozwiązań automatyzacyjnych z ręcznymi.
Wysokie regały pozwoliły efektywnie wykorzystać przestrzeń magazynową. Zautomatyzowany proces składowania jest niezawodny, a wózki automatyczne sprawdzają się w ciągłej pracy, pozwalając zwiększyć przepustowość magazynu bez konieczności zwiększania zatrudnienia. – Z naszej perspektywy zastosowane rozwiązanie jest optymalnym połączeniem automatyzacji i zadań realizowanych przez operatorów. Dzięki funkcjonalnościom takim jak: opcjonalne przełączanie pomiędzy ładowaniem okazjonalnym a wymianą akumulatorów czy też przydzielanie wózków do pracy w określonych strefach, jesteśmy w stanie modyfikować funkcjonowanie systemu pod kątem aktualnych potrzeb – mówi Paweł Spyrka, kierownik magazynu Lajkonik Snacks. – Wdrożone rozwiązanie w pełni spełniło nasze oczekiwania. W najbliższej przyszłości planujemy dalszą współpracę z firmą STILL w zakresie automatyzacji procesów intralogistycznych w naszej firmie – podsumowuje.
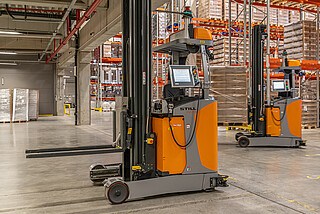
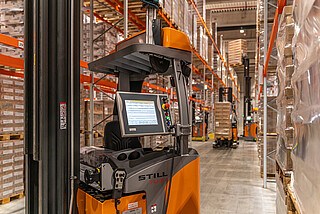
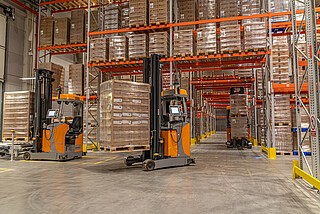