Tarkett: automatyzacja dla wydajności
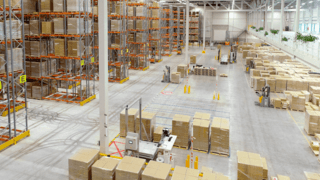
Dzięki wdrożeniu regałów wysokiego składowania i systemu automatyzacji w nowym centrum dystrybucji firmy Tarkett udało się znacząco zwiększyć liczbę miejsc paletowych i przepustowość magazynu bez konieczności zwiększania zatrudnienia.
Na skróty:
Firma Tarkett wyrosła ze swojego dotychczasowego centrum dystrybucji – w sezonie potrzebowała nawet dwukrotnie więcej miejsc paletowych niż pozwalał na to stary obiekt.
- Poszukując nowego sposobu organizacji gospodarki magazynowej, zwróciła się do pomoc do firmy konsultingowej Groenewout, która stworzyła 5 scenariuszy.
- Ostatecznie firma Tarkett zdecydowała się na wdrożyć regały wysokiego składowania w układzie VNA oraz system automatyzacji procesów transportu wewnętrznego dostarczone przez firmę STILL
- W efekcie udało się zwiększyć liczbę miejsc paletowych i przepustowość magazynu bez konieczności zwiększania zatrudnienia.
Charakter przedsiębiorstwa, w którym dokonano wdrożenia
Nazwa: Tarkett
Obszar działalności: Produkcja pokryć podłóg
Miejsce wdrożenia: centrum dystrybucyjne Waalwijk, Holandia
Firma Tarkett to międzynarodowa spółka zajmująca się produkcją pokryć podłóg – zarówno do zastosowań w przestrzeniach mieszkalnych, jak i obiektach użyteczności publicznej. Firma ma w ofercie wykładziny, płytki, panele, linoleum, posadzki drewniane i laminowane – w tym do specjalistycznych zastosowań, m.in.: systemu ochrony zdrowia czy powierzchni handlowych. Przedsiębiorstwo sprzedaje w skali roku pokrycia podłóg o metrażu około 1,3 mln mkw. i wartości około 2,6 mld euro. W 36 zakładach i oddziałach krajowych Tarkett zatrudnia w sumie 12,5 tys. osób. Ważnym elementem polityki przedsiębiorstwa jest poszanowanie zasobów oraz stała poprawa bezpieczeństwa pracy. W duchu tych strategicznych celów firma dokonała ostatnio automatyzacji procesów transportu wewnętrznego w centrum dystrybucyjnym w holenderskim Waalwijk.
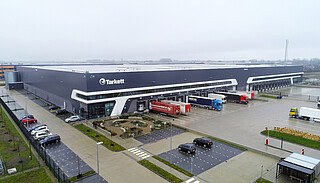
Cel wdrożenia oraz zastosowane rozwiązania intralogistyczne
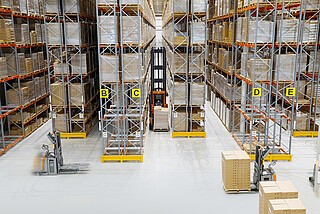
Cel wdrożenia:
- Zwiększenie przepustowości magazynu i maksymalnej liczby miejsc paletowych
- Ograniczenie kosztów gospodarki magazynowej w wysokim sezonie
- Zażegnanie sytuacji, w której wzrost natężenia ruchu i zapełnienia przestrzeni mogłyby powodować spadek poziomu bezpieczeństwa
Wdrożone rozwiązanie intralogistyczne:
- nowe, zaprojektowane od podstaw zautomatyzowane centrum dystrybucji
- zintegrowane z systemem WMS automatyczne wózki systemowe STILL MX-X iGo systems oraz samojezdne wózki podnośnikowe STILL EXV iGo systems do obsługi i zaopatrzenia regałów wysokiego składowania w układzie VNA
- sterowane ręcznie wózki unoszące z platformą dla operatora STILL EXU-S oraz wózki wysokiego składowania STILL FM-X do rozładunku i załadunku oraz obsługi regałów na niestandardowe ładunki
Przed przeprowadzką i modernizacją centrum w Waalwijk było przystosowane do składowania około 1 mln mkw. płytek podłogowych. Główną motywację do znalezienie nowego miejsca i wprowadzenia bardziej wydajnych rozwiązań stanowił fakt, że w wysokim sezonie potrzeby magazynowe były około dwukrotnie wyższe. W związku z tym istniała konieczność okresowego korzystania ze składowania zewnętrznego oraz adaptacji powierzchni zakładu produkcyjnego w belgijskim Dendermonde. Komplikowało to łańcuch dostaw, niosło ryzyko opóźnień i – wbrew polityce zrównoważonego rozwoju firmy – podnosiło środowiskowe i finansowe koszty obsługi ładunków. – Krok, który zdecydowaliśmy się podjąć, był konieczny, by zwiększyć bezpieczeństwo naszych procesów. Wyrośliśmy z naszego starego obiektu i korzystanie z niego w niezmienionej formie mogło prowadzić do potencjalnie groźnych sytuacji – mówi Michiel van Trijen, Supply Chain Manager EMEA w Tarkett. – Mieliśmy więc wiele powodów, by dowiedzieć się, jak zorganizować nasze procesy w bezpieczniejszy, bardziej niezawodny i efektywniejszy sposób – dodaje. Podjęto decyzję o przenosinach do większego obiektu i skorzystaniu z usług doradczych firmy konsultingowej Groenewout zajmującej się optymalizacją w logistyce. Konsultanci opracowali w sumie pięć
scenariuszy dalszego rozwoju centrum. Jako najodpowiedniejsze rozwiązanie wybrano ostatecznie wynajęcie obiektu o powierzchni 14 tys. mkw. w nowym Parku Prologis w Waalwijk z certyfikatem BREEAM Very Good i wprowadzenie na niej systemu regałów z bardzo wąskimi alejkami obsługiwanego przez wózki automatyczne. Holenderski oddział STILL dostarczył Tarkett podzielone 21 korytarzami roboczymi systemy regałowe wysokiego składowania, jak i 6 automatycznych wózków odpowiednich do obsługi tej strefy oraz jej zaopatrywania. Po wskanowaniu ładunków w system WMS samojezdne wózki podnośnikowe EXV iGo systems dowożą towar ze stref buforowych do punktu przeładunkowego w sekcji VNA, skąd pobierane są one przez automatyczne wózki systemowe MX-X iGo systems i umieszczane zgodnie ze wskazaniami WMS na regałach wysokiego składowania. Tymi samymi środkami w zautomatyzowany sposób realizowany jest także proces kompletacji. Z użyciem sterowanych ręcznie przez operatorów wózków unoszących EXU-S ze stałą platformą odbywa się rozładunek, wskanowanie przychodzących dostaw w system WMS i załadunek zamówień. W obsłudze regałów w dwóch alejkach przeznaczonych na niestandardowe ładunki zastosowanie znajdują natomiast załogowe wózki wysokiego składowania serii STILL FM-X.
Efekty wdrożenia i wynikające z niego korzyści
Uzyskanie w obiekcie dużej gęstości składowania
- Zwiększenie wydajności procesów i wyeliminowanie dodatkowych kosztów wynikających z tworzenia magazynów otwartych i korzystania z innych placówek w wysokim sezonie
- Poprawa bezpieczeństwa pracy dzięki automatyzacji i klarownemu wyodrębnieniu poszczególnych stref centrum dystrybucji
- Częściowe uniezależnienie się od sytuacji na rynku pracy dzięki ograniczeniu zaangażowania operatorów w obsługę wózków widłowych
Zaproponowane i dostarczone przez holenderski oddział STILL rozwiązanie – system automatyzacji transportu wewnętrznego w oparciu o regały wysokiego składowania podzielone bardzo wąskimi alejkami oraz strefy rozładunku, załadunku i buforowe z wózkami sterowanymi ręcznie – pozwoliło uzyskać Tarkett dużą gęstość składowania pozwalającą na bezproblemowe zmieszczenie w obiekcie 18 tys. miejsc paletowych. Dzięki automatyzacji procesów transportu wewnętrznego znacząco zmniejszono liczbę zadań wymagających zaangażowania operatorów – co ma zasadnicze znaczenie w kontekście niedoborów wykwalifikowanych pracowników. Klarowne wyodrębnienie stref pracy automatycznej, korytarzy roboczych obsługiwanych przez wózki sterowane ręcznie oraz obszarów ruchu pieszych pozwoliło zminimalizować ryzyko wypadków. Ograniczono także liczbę błędów i poprawiono efektywność pracy. – Udało się nam zrealizować założenia odnośnie oszczędności – mówi Supply Chain Manager EMEA w Tarkett. – Wierzymy, że optymalizacja pozwoli nam utrzymać wiodącą pozycję na konkurencyjnym rynku, na którym działamy – dodaje Van Trijen. Centrum dystrybucyjne w Waalwijk służy jako modelowe case study automatyzacji dla kolejnych obiektów Tarkett. Wstępne plany przewidują, że kolejne wdrożenie uda się zrealizować jeszcze w tym roku.
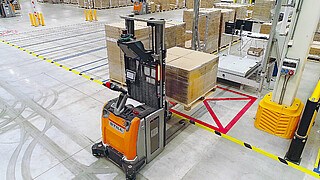